国金证券近日发布锂电池硅负极深度报告:能量密度的提升是电池发展长期趋势,负极环节对应趋势则为硅负极,CVD硅碳的应用大幅加速硅负极产业化,在手机等消费类市场硅负极已迈过0-1,25年预计进一步放量,在车用市场25年有望实现产业化0-1。
以下为研究报告摘要:
核心观点:CVD硅碳工艺的出现大幅提速硅负极的产业化,25年硅负极预计在手机领域扩大渗透,也有望在动力场景实现0-1,我们建议关注硅负极放量背景下,新工艺带来的产业链增量环节投资机会。
CVD法硅碳成新主流工艺,加速硅负极产业化,重塑竞争格局。1)球磨法向CVD法迭代:在硅的纳米化工艺上,CVD法能将硅径粒精确控制在10nm以内,并实现均匀包覆,取代球磨法成为新一代主流工艺;2)CVD硅碳相比硅氧优势扩大:目前CVD法硅碳/硅氧产品的克容量约1800/1500mAh/g,且CVD硅碳可支持超1000次循环,并实现低于硅氧的膨胀水平。3)新工艺重塑格局:CVD法下工艺、设备较硅氧大幅迭代,重塑先前硅氧的竞争格局,当前天目先导、兰溪致德、璞泰来、贝特瑞等在CVD硅碳进展领先。
成本:中期向石墨负极靠近,多孔碳、设备仍有较大降本空间。硅负极成本构成中由高到低分别为多孔碳、硅烷气、设备。我们假设当前采用高性能树脂多孔碳,中期采用生物质多孔碳,价格从50万/吨降至15万/吨;硅烷气从9万/吨下降至7万/吨;单吨制造成本从6.5万/吨下降至3.5万/吨,则测算CVD硅碳负极的成本有望从当前40-45万/吨下降至中期15-20万/吨,硅碳负极价格有望持续向石墨负极靠拢。
市场:消费场景先落地,动力迈向0-1。1)小动力:高倍率小圆柱电池已开始应用硅负极;2)手机:25年手机迈向7000mAh时代,苹果、华为、荣耀、小米等品牌已/将推出硅负极机型,硅负极从高端机向中低端渗透;3)电车:特斯拉、宝马大圆柱电池明确搭载硅碳负极,25年部分国内新能源高端车型有望应用硅负极;4)固态&半固态电池:未来有望在车、手机、低空等领域逐步落地应用,掺硅量较其他场景更大。我们预计到28年全球硅负极需求4.5万吨,假设30万元/吨,对应市场135亿元,其中小动力/手机/电车/固态&半固态电池对应需求0.28/0.09/3.4/0.75万吨。产业链:多孔碳迈向规模化0-1,硅烷市场大幅扩容,PAA、CNT打开新应用场景。
1)多孔碳:迈向规模化0-1,树脂/生物质路线构成主流。伴随CVD硅碳的应用,多孔碳预计迈向规模化0-1,未来看好双路线并行发展,预计生物质路线发挥成本优势,在低端市场占据主导,通过性能提升向中高端市场渗透;树脂路线则依靠性能优势占据高端市场,通过降本向下渗透,国内代表企业分别为元力股份、圣泉集团。
2)硅烷气:预计市场大幅扩容。我们测算24年国内合计电子级硅烷气需求约1.26万吨,预计28年硅基负极对应硅烷气需求约1.9万吨,规模为现有市场的1.5倍,大幅扩容,国产企业中硅烷科技等产能领先。
3)粘结剂&导电剂:PAA、CNT打开新应用场景。粘结剂控制硅负极的体积膨胀,PAA有较优的力学性能和拉伸强度,且应用后有较好的库伦效率,国内茵地乐在PAA份额领先;需添加导电剂确保硅负极的导电性,加入单臂碳纳米管大幅改善循环性,国内天奈科技布局进展领先。
投资建议与估值
能量密度的提升是电池发展长期趋势,负极环节对应趋势则为硅负极,CVD硅碳的应用大幅加速硅负极产业化,在手机等消费类市场硅负极已迈过0-1,25年预计进一步放量,在车用市场25年有望实现产业化0-1,建议关注硅负极企业及上游的多孔碳、硅烷气、粘结剂、导电剂等环节。
风险提示
技术迭代风险,硅负极降本不及预期,硅负极性能提升不及预期。(国金证券 姚遥)
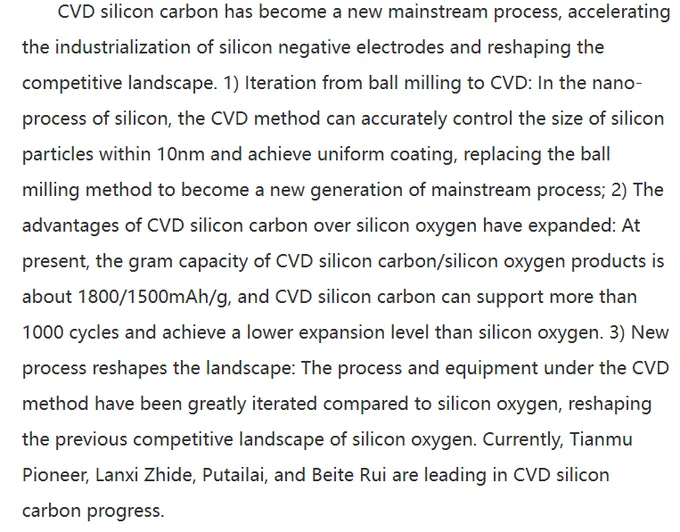
Hi ryan, i’ve spent a lot of time of this, professionally, and the whole smartphone industry will clearly be silicon carbon in about two years, Apple is going to put it in the next iPhone, I will bet you a burger, with nothing on it!
I think there is some confusion here. First, you mentioned Si-based anodes (Si-C in this case) made using CVD. There are two companies who do this commercially, one is Amprius, and the other is Leyden Jar. Both make pretty good batteries.
But, and this is a big BUT here, the process of making Anode rolls using PECVD or PVD is up to 10 times more expensive than making rolls using conventional powder coating using die slot coating and calendaring.
Next you mention Group14, who is a raw powder supplier. And yes, they use carbon pyrolysis followed by silane infusion to make the powders.
Lots of batteries have been using powder based active silicon as an additive to graphite in the anode. In production, I’ve seen figures showing that some companies use up to 6-8% of active silicon powder in addition to graphite.
In the lab, some companies have claimed that they can up that number to 40%, but no one has claimed that they can make these batteries work in a production process yet, that I know of.
Enovix does not use CVD or PVD in their anode process, they use standard coating. So they can use any powder that they can buy. The powder could be made using PVD or CVD, but those are too expensive this far. If someone is able to produce cheap CVD powder, then Enovix will be able to use it.
The difference between Enovix and everyone else is that they can put 100% of these powders in their batteries. Not just 8%. The Enovix architecture controls swelling so they can use more active silicon.
But more that just controlling swelling, the architecture allows for more effective pre-lithiation. So even if another battery company could put more silicon in their batteries, they could not pre-lithiate the batteries in production.
Lastly, the geometry of the ENVX architecture allows for more efficient packing of anodes and cathodes, especially as the batteries get smaller. This increased the amount of material that can be used and alone accounts for increases in energy density. I don’t know why the Group14 material and CVD silicon were conflated in this discussion, but it doesn’t seem to make sense.
The fact is that Group14 material is in millions of smartphones today, they are sampling with the entire battery industry and ramping output 50x to meet demand. The industry might find better ways to improve in future but as is, Si-C is the winner already.
Interview: Group14 CEO Rick Luebbe on why silicon batteries can ‘electrify everything’
CNME Editor Mark Forker sat down with Rick Luebbe, CEO and Co-Founder of Group14, to hear how his company is …
By Mark Forker
8 min. read
View original
CNME Editor Mark Forker sat down with Rick Luebbe, CEO and Co-Founder of Group14, to hear how his company is ushering in a new era of silicon batteries, and how the technology can power both the electrification movement globally, and be an enabler for AI technology.
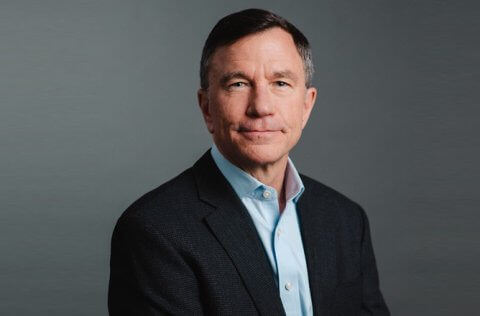
Rick Luebbe is a US entrepreneur that has spent the last 20 years developing solutions and products that are designed to transform the energy sector.
In a decorated and distinguished career, Luebbe has established himself as a prominent business leader in the renewable energy space.
Prior to carving out a successful career as an entrepreneur, Luebbe served in the US military.
Nowadays, he is currently the CEO and Co-Founder of Group14, which is on a mission to ‘electrify everything’.
Luebbe is a firm believer that silicon batteries will be the key cog in that electrification effort.
However, Luebbe began our conversation by giving a broader overview on his two decades in the energy industry, and the factors that led to the creation of Group14 in 2015.
“The parent company of Group 14 was called EnerG2. We founded EnerG2 back in 2003, and at the time my co-founders and I looked at a whole bunch of different business opportunities, and we recognised that being entrepreneurs consumes a lot of life energy, so we decided that we wanted to pour our life energy into something which we would feel really good about, win, lose, or draw. We just wanted to feel that we were pushing the ball in the right direction. This led us down the path of renewable energy, which in 2003, was well before the clean tech initiative kicked into gear. We looked at a number of different opportunities, but the first project that we really started to get excited about was hydrogen storage, which 20 years later is becoming popular again. In 2003, that was the next big thing and the prediction was that we were all going to be driving in hydrogen-powered vehicles by 2010,” said Luebbe.
As Luebbe explained the science behind it was of a paper-based nature, which as it turned out was not going to work, but their technology platform was still able to be incredibly intuitive and innovative, which ultimately led them down the path towards silicon batteries.
“We were really excited about using synthetic nano carbons for storing hydrogen based on a paper nature. It turned out that the paper was debunked and wrong, but we didn’t know that at the time. However, the technology platform was really interesting, and we did a lot with it. We made carbons for ultra-capacitors, and we made carbons for additives for elastic batteries to make them work better. Through that path we became very interested in improving the performance of lithium-ion batteries, and using our platform to make silicon work in batteries using this carbon platform. Once we realised just how effectively we could improve silicon performance, we took all our key resources and spun that out of EnerG2 and then sold EnerG2 to German chemical company BASF in 2016. That acquisition then led us down this concentrated path on silicon batteries, which has been brilliant for us,” said Luebbe.
Luebbe conceded that when it comes to the electrification movement across the United States, there is rather inevitably some resistance to change, it is human nature after all for us to not like change.
However, as Luebbe explained, the fact that silicon batteries can generate up to 50% more energy than a traditional high-performance lithium-ion, means that in all reality it is a gamechanger for a lot of key industry verticals.
“Silicon battery technology became so compelling to us, and our mission, which is to electrify everything, became real. It’s great to have support from governments and subsidies that are designed to accelerate electrification, but change is hard as we know. I believe the fact that silicon batteries are so compelling that it is going to happen anyway. The performance differential that you get with a silicon-based storage system over a traditional system is a gamechanger. Silicon batteries originally focused on providing more energy, and our technology can provide 50% more energy than traditional state-of-the-art high-performance lithium-ion batteries–that’s really exciting for consumer electronic products, and for the aviation industry because range and weight really matters,” said Luebbe.
Luebbe also added that in the last couple of years they have discovered that silicon batteries fundamentally charge fast.
“We have one customer that can go from 0-100% state of charge in 90 seconds, and that’s unbelievable. In Dubai, Joby is establishing two Vertiports, and Joby will manage the charging system. If it’s not a silicon-based charging system then those aircrafts may have to sit there for 5-6 hours to become fully charged, but if you can charge those planes in 5-6 minutes then it really enables the commercialisation of electric aviation. The energy benefits are awesome, but where I believe the fundamentally transformational element with silicon batteries will come is in their ability to enable fast charging,” said Luebbe.
A major barrier in the mass adoption of electric vehicles, not only in the US, but across most key markets globally is the issue of ‘charge anxiety.
Again, as Luebbe points out, a solution to all these issues are silicon-based charging systems.
“The major stumbling block in the EV adoption marketplace is charging. I drive an EV, and I love it, and it’s a big robust vehicle that can do 0-100 in 3 seconds, but if I want to charge it, then it takes around 45 minutes. This is far too long for the average consumer. The average fuel stop in the United States is 8 minutes. Charge anxiety is the primary inhibitor in the electrification of transportation, but if we can get that charge time down to less than the current stop time for internal combustion then that anxiety goes away completely. In addition to this, if you can get a car in and out of a charging system in 5 minutes then you don’t need as many chargers, and a reduction in infrastructure also translates to a reduction in overall investment costs.
Considering everything Luebbe has outlined about silicon batteries, it begs the question as to why there hasn’t been mass adoption of silicon batteries. As Luebbe explains, there is a constraint when it comes to silicon materials, but that will soon change when their purpose-built factories kick into full operation.
“The only constraint in why there hasn’t been a mass adoption of silicon batteries is the availability of silicon battery materials. We’re the most advanced when it comes to other companies operating in the silicon battery space, and we’re building a factory in Moses Lake in Washington State, which we expect to come online in Q1. That factory’s initial annual capacity will be about 2,000 tons or 10 GWh of silicon battery material, which translates into around 100,000-200,000 EVs per-year. We have a commercial facility for consumer electronics, but it can only make about 2% of what the factory in Moses Lake is going to deliver. Our material is already in millions of cell phones because obviously they don’t require as much material or as big a battery as an EV does. The factory we’re building is really what is required to drive the transformation that is needed. In the meantime, we have a joint-venture factory with SK in South Korea which is similar to the one we are constructing in Moses Lake. That joint venture factory began shipping in August 2024. The silicon battery era is just beginning with these facilities that are capable of providing enough material for those who want to move to a silicon strategy,” said Luebbe.
Luebbe said that the silicon battery era only really began in September 2024, but he can see a demand for the technology from the huge volume of customers they have already acquired.
“We have over 110 customers currently in qualification, so virtually everyone in the industry, and that is for two reasons. One, the material works, and it really does improve battery performance significantly. And we are the only ones that can produce at the kind of scale needed to get to that breadth of customer base. Our technology is a complete drop-in for current battery manufacturers, so it is very easy to switch from traditional to lithium-ion, and it processes the same that graphite does today. For example, let’s say Tesla has a 30-hour gigawatt factory in Nevada, they could theoretically switch to a silicon-based anode overnight and get a 50% improvement in energy density in those cells. If we can improve the cell by 50% then we have increased the capacity of that factory from a 30 gigawatt-hour to a 45 gigawatt-hour factory, with no CAPEX. There are also huge benefits from a cost perspective, so all-in-all it’s a gamechanger and a no-brainer to pursue a silicon-based battery approach,” said Luebbe.
AI is the name of the game, and feels like in many ways is the only currency in town.
It is dominating the tech landscape, but Luebbe believes that silicon batteries can also be an enabler in the AI era.
“Silicon could be an enabling technology for AI. We know that the new AI models consume a lot of energy. At the consumer device level, our material is now powering AI-enabled smartphones made by Honor in China. These AI-enabled chips consume a lot more power, and the dilemma is that you don’t want to trade one feature for another, so there’s no point having these AI-powered chips if you can only run your phone for 10 hours as opposed to 18 hours, consumers don’t want that. Silicon batteries give more energy density in the cell and they don’t have to make the battery bigger as a result, and now they can balance that run time with this new AI capability, and deliver the same user experience for the consumer. That’s one of the really attractive aspects of a silicon battery in consumer electronics,” said Luebbe.
In addition to this, he concluded a brilliant exchange by outlining how silicon can be a remedy to the issues facing AI-powered datacentres globally.
“AI-powered datacentres require huge peaks of power when they are going through a specific processing surge. In order to accommodate these peaks, datacentres have to leave a whole bunch of excess power effectively on standby in order to absorb those peaks. What that essentially means is that they can’t put as many servers in that datacentre as they would like, and as a result almost every single datacentre is power constrained. One of the advantages of silicon batteries is that they charge fast as we talked about, but they also discharge fast too. So now you can put in at the rack level silicon batteries to absorb those power peaks, and that will enable your datacentre to have more capacity and get more utility out of that infrastructure,” concluded Luebbe.
Leave a Reply